Control of the Tundish Superheat by Modeling the Temperature Loss After the Final Secondary Refining Process Step Using a Machine-Learning Approach
机器学习模拟精炼后温降控制中间包过热度
中间包内钢水过热度保持在一定的温度范围内,对连铸过程的稳定性、铸坯的质量和连铸机的生产率都是至关重要的。因此,在精炼工艺过程的最后一站的钢包内钢水温度调整是控制中间包过热度的关键。在目前的工作中,利用各种机器学习技术,基于精炼参数、钢包条件和连铸参数对温降进行了建模,并将该模型作为实时计算集成到二级在线过程控制系统中。将中间包钢水过热度保持在一定的温度范围内,对保证连铸过程的稳定性、生产效率和铸坯质量至关重要。与目标偏差较大的过热度可能导致连铸漏钢、浸入式水口(SEN)堵塞、铸坯鼓肚、结晶器液位变化、中心偏析明显、连铸拉速降低、连铸中断等事故。中间包内的钢水温度必须高于液相温度,这是由特定钢种的化学成分来决定的。根据钢种的不同,目标过热度在10到35°C之间进行调节。在连铸过程中,由于钢包内部温度的不均匀性和连铸过程中固有的温度损失,过热度可能会发生变化。然而,钢水过热度必须保持在一定的温度范围内(见图1),这样才能对铸坯产品的质量和铸机生产顺行有利,减少或消除负面影响。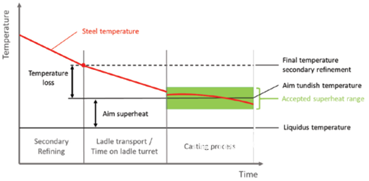
图1 钢水的温度随时间的变化在精炼结束和连铸结束之间温度曲线(第一列:红色的是钢水温度,温度损失,二次精炼;第二列:目标过热度,钢包吊运/钢包在回转台上等待时间‘第三列:连铸过程;第四列:最终的精炼结束钢水温度,中间包目标钢水温度,可接受中间包钢水过热度范围,液相线温度)因此,在二次精炼工艺过程的最后一站,钢包内钢水温度的最终调整是建立中间包过热度的关键。如图1所示,最终温度的计算需要考虑从精炼过程结束到连铸机钢包回转台就位开浇时刻的温度损失,这取决于各种工艺参数,一般是非线性关系。钢包和中间包内钢液温度的预测可以通过各种模型方法来实现。基于基本传热方程(第一原理)的数值模型是由Xia和Ahokainen,[1] Ferreirat团队[2], Gupta和Chandra[3], Samuelsson和Sohlberg[4], Wu团队[5], Zabadal团队[6],和Gastón团队[7]开发的。这些模型通过理论手段描述了观察到的现象,考虑了表征过程的基本物理和化学定律,并附加了工艺过程参数,其值必须通过试验和测试获得。随着计算能力的提高,计算流体动力学(CFD)也被应用于这类问题(Jormalainen和Louhenkilpi[8],Tripathi[9])。另一方面,黑箱模型使用纯统计方法(Sonoda等人[10])或基于机器学习算法的方法(Laha等人[11],Klanke等人[12],Wang等人[13],Hou等人[14]和Jo等人[15])。灰盒模型结合了第一原理和统计模型方法,由不同的研究人员开发并成功应用(Psichogios和Ungar[16], Okura等人[17], Tian等人[18]和Ahmad等人[19])。这种类型的模型方法允许用第一性原理模型计算已知的线性或非线性现象,另一方面,使用统计模型对未知关系进行建模。一般来说,灰盒模型比简化的第一原理模型更精确,比CFD模型消耗的时间和资源少得多,比纯统计模型更容易解释。得兴泰纳巴西钢厂,在这个描述模型的实现之前,最终精炼站钢水温度计算是基于纯粹的经验方法,根据最后精炼站到连铸钢包回转台之间的吊运时间计算钢包散热损失,考虑钢包使用历程状态(例如受钢钢包状态:温度很低的钢包,较低温度的钢包,温度尚可的钢包和高温钢包),以及相关与砌筑耐材钢包承载第一包钢水和中间包第一包钢水浇铸等信息。通过应用现在的模型精细调整,约80%的铸坯可以在既定的过热度范围内进行生产。然而,即使对可用的经验参数进行不断调整,这个百分比也不能显着提高,因此说明了这种模型方法的技术局限性。为了详细阐述一个包含额外工艺参数的更复杂的模型,必须对钢厂内部的钢包循环进行简要讨论,如图2所示。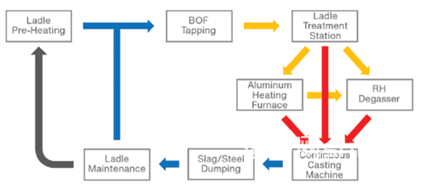
图2 巴西得兴泰纳Ternium公司炼钢厂钢包循环示意图(钢包循环:钢包维护准备→钢包烘烤→转炉出钢→钢包炉精炼处理→RH真空脱气处理或铝加热炉或直接进入连铸机→倒渣)在钢包烘烤器预热钢包耐材中,砌筑后的钢包要烘烤预热几个小时时间,以避免耐火材料受到过大的热冲击,从而形成裂纹,在砌筑后冷钢包预热后接受第一包钢水时候要考虑钢水温降较大。转炉(BOF)出钢过程中,钢包内填充钢液,因此钢包耐材得到进一步加热,出钢后,钢包吊运到精炼设备进行精炼,有几种工艺路线可能,如图2中橙色标记。巴西泰纳钢厂配备了一个钢包处理站(LTS),在那里调整化学成分,吹氩处理为钢包提供必要的成分和温度的均匀化。从LTS站,该钢包中这炉钢水可能已经准备好用于连铸浇钢,或进一步吊运到铝加热炉(AHF)进行合金化和温度调整,或吊运到RH脱气器进行真空处理、合金化和温度调节。在最后一次精炼处理后,将钢包吊运到连铸机钢包回转台上(图2中红色标记)。在这个钢包吊运和在连铸机钢包回转台上进一步等待的时间,直到钢包最终开浇,钢包的温度由于散热造成钢水温度下降,这可以本工作中模拟出来的。浇铸完毕钢包开浇机构关闭后,钢包回转台旋转到受钢位置,行车将钢包内剩余的钢和炉渣倾倒掉,将钢包吊运到钢包维修站,在那里进行钢包清理和钢包滑板开浇机构维修。在此维护程序结束后,钢包再次被吊运回转炉准备接受出钢,或者,如果钢包等待接受钢水时间过长(例如在日常钢厂维护日),钢包就要被移到钢包烘烤器上烘烤预热。在目前的工作中,根据图2所示的钢包周期的工艺参数,包括时间跨度、钢包寿命、精炼和连铸参数,使用各种机器学习技术对图1中的温度损失进行了建模。本文概述了该模型的数据采集和建模过程、测试,最后给出了模型的实际应用和实践。数据过滤和参数关联
在这项工作中,学习处理了18个月的生产的炉号和连铸板坯有关的数据,应用如图3所示的过滤步骤,生成模型开发和测试所依据的数据集。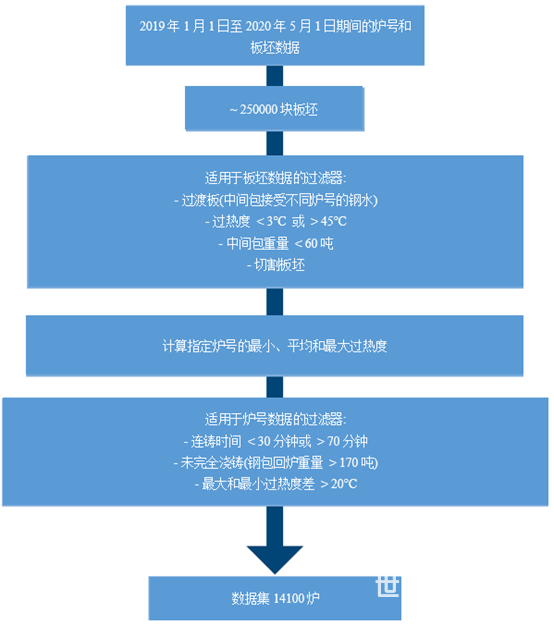
图3 准备数据集的步骤作为第一步,从制造执行系统(MES)收集了大约25万块板坯的连铸过热度数据,然后进行过滤,以保证过热度信息的正确性。这是通过过滤掉过渡板坯来实现的,在过渡板坯中,序列中的前炉号或后炉号的钢水仍然存在于中间包中,以及过滤掉中间包重量低于60吨的生产的板坯,因为在这种情况下,无法保证钢水连续测温装置的完全浸入。测量到板坯过热度远远超出操作允许范围,这可能表明测量出现问题,也被过滤掉。此外,由于纵向切割一个炉号的板坯产生多次信息,会在数据集中出现多次,因此要排除掉这些重复数据。根据基于板坯的过热度信息,计算出各炉号的最小过热度、平均过热度和最大过热度以及过热度度的标准差。仅部分连铸或连铸时间超出设定的标准(仅用两流铸机铸机一流数据)的炉号在第一步中被过滤掉。随后,对中间包过热度最大值与最小值之差数据进行分析,如图4所示。
图4 根据顺序位置(中间包炉号计数器)和浇铸时间,每炉测量的中间包过热度最大值和最小值之间的平均差(a)和标准偏差(b)从图4a可以看出,中间包接受第一炉钢水时测得的过热度最大值和最小值之差的平均值在7℃左右,而在后续的连续炉号浇铸中,过热度的平均值明显更低,这是有道理的,因为中间包在这种情况下其耐材没有得到充分预热,因此需要从钢水吸收大量的热能来加热中间包耐火材料。钢包平均差随着浇铸时间的增加而增加,因为热量通过钢包壁不断散失。图4b显示,中间包受钢第一炉测得的过热度最大值和最小值之差的标准偏差约为5°C,随后的连续炉浇铸时约为3°C。由图4a和图4b可知,测量过热度最大值和最小值之差大于20℃的炉号可能存在测量误差等,因此可以过滤掉。下一步,使用如图3所示的约14100炉的清晰的数据集,对最终精炼炉的相关工艺参数与测量的最终温度进行相关性分析。分析结果为计算出各工艺参数的线性相关系数,如图5所示。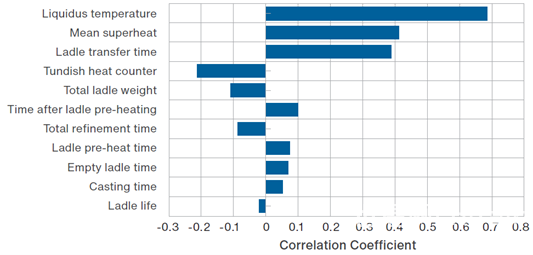
图5 各工艺参数与最终精炼炉温度之间的线性相关系数(纵坐标从上至下:液相线温度,平均过热度,钢包吊运时间,中间包连浇炉数,钢包总重,钢包烘烤预热后到出钢时间,总体精炼时间,钢包烘烤时间,空置钢包时间,浇铸时间,钢包寿命)由于中间包内钢水温度由钢种的液相温度和过热度组成(见图1),可见这两个参数的相关系数最高。在分析中,采用了基于目标化学成分的液相线温度和中间包比热来测量过热度的平均值。钢包吊运过程中的温降与钢包从最后精炼炉到连铸机所需时间成正比,相关系数第三大。这个吊运时间表示从钢包离开精炼炉到钢包落在回转台上后旋转到位,然后打开开浇机构的滑板开浇之间的时间。如图4a所示,中间包接受第一炉钢水时候带走了很多热能,降低了钢水温度,因为在巴西泰纳钢厂中间包没有烘烤预热。因此,中间包炉号计数器是一个具有负相关系数的重要参数。钢包总重量,即钢水重量和钢包重量(即钢包钢结构和耐火材料)的总和,是下一个最重要的工艺参数。钢包越重,热量损失越低,最终需要调整的温度也越低。模型参数“烘烤预热后时间”测量的是空钢包离开烘烤器到出钢过程结束之间的时间(见图2)。时间越长,热损失越大,因此需要调整的最终温度也越高。在没有钢包烘烤预热的情况下,该值读为零。总精炼时间表示从出钢过程结束到钢包离开最后一个精炼站之间的时间,这个时间越长,钢包耐材被加热得越好,因此热量损失越低。烘烤预热时间与钢包到达烘烤器的热状态成正比。一般来说,烘烤预热只在冷钢包进入循环或钢厂长期停产后进行。此参数与烘烤预热后的时间一致。“空钢包时间”是指钢包在连铸回转台处关闭钢包的滑板时刻和出钢过程结束之间的时间(见图2)。钢包在循环中没有钢水的时间越长,最终温度必须调得越高。如图1所示,并根据图4a的测量结果表明,过热度随着浇注时间的增加而降低,浇注时间表示钢包在回转台处开浇和关闭滑板之间的时间。在预测最终温度时也必须考虑到这种热损失。本研究中考虑的最后一个参数是钢包寿命,它代表钢包经历的循环次数。猛然一看,负相关系数是违反直觉的,因为人们可能会期望耐火材料的侵蚀随着钢包寿命的延长而加重,因此热损失应该更高,因此,最终温度必须调整得更高,这应该用正相关系数来表示。然而,由于先进的耐火材料侵蚀轻,在保持相同中间包自由空间的情况下,更多的钢包体积可用,因此已经讨论过的较高钢包重量的影响(略微)胜过耐火材料侵蚀的影响。建模
最终精炼站的钢水温度使用KNIME分析平台,基于图5中已经讨论过的11个工艺参数的数据集,通过应用各种标准机器学习算法,即多项式回归,人工神经网络,梯度增强树回归和随机森林回归,进行建模。与模型类型无关,对数据集进行归一化处理,以常用的80%/20%的比例分割为训练和验证数据集。训练过程还包括使用爬坡算法进行超参数优化。各模型类型调整后的决定系数R2和平均绝对误差列于表1。表1 调整后的决定系数R2和各模型类型的平均绝对误差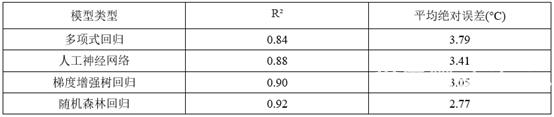
最简单的模型方法是3阶多项式回归,其平均绝对误差为3.79℃,调整后的决定系数R2为0.84,对于这种简单的模型方法来说,这是一个很好的结果。使用一个隐藏层和六个节点的人工神经网络可以获得相当好的结果。如表1所示,使用涉及决策树的模型可以获得最佳结果。两种模型的R2系数均≥0.9,平均绝对误差接近甚至低于3℃。预测误差如图6所示,累积炉号数作为预测误差的函数。使用随机森林回归模型,超过90%的验证数据集的温度被预测,最大误差在5到6℃之间。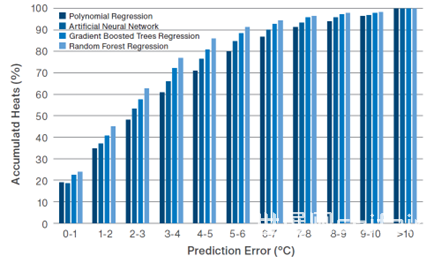
图6 根据预测误差和模型类型分组验证数据集的累积炉号数(表1中4种模型方法)实测和预测的最终温度对比如图7所示。值得注意的是,与其他模型方法相比,随机森林回归显示>10℃的“主要”异常值较少,绘制的点也更“靠近”于45°线。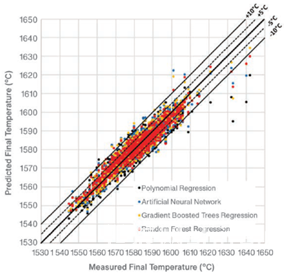
图7 最终测量温度与预测温度的比较。虚线表示±5℃范围,实线表示±10℃范围实施
随机森林回归模型作为Python脚本在精炼过程二级自动化系统中实现,脚本在精炼站的最后执行,以计算最终钢水温度的设定值。模型的输入参数必须与静态参数分开,静态参数在计算之前已经知道,不会再改变,例如:液相线温度和目标过热度;中间包炉数计数器;钢包总重量;钢包烘烤预热时间和烘烤器到出钢开始的时间;空钢包时间,钢包寿命;以及动态参数,这些参数在正在进行的精炼过程中可能会发生变化,因此只能根据钢厂的生产计划作为预测参数,例如:精炼时间。钢包吊运时间。连铸时间。每当其中一个动态参数发生变化时,必须再次执行模型,并相应地更新最终温度的设定值。需要指出的是,该模型只计算温度设定值。与中间包过热度有关的实际模型性能仍取决于操作因素,例如:精炼过程结束时钢包最终温度的实际值与模型计算的目标值之间的偏差。精炼时间、钢包吊运时间和连铸浇铸时间的预测值与实际值之间的偏差。精炼过程结束时最终温度或中间包温度的测量误差。结论
为了将中间包过热度保持在一定的温度范围内,从而保证连铸机的生产效率和产品质量,利用KNIME分析平台开发了精炼过程中钢包钢水最终目标温度的机器学习模型。将所建立的模型应用于试验数据,调整后的决定系数R2>0.9,平均绝对误差小于3℃。该模型在二级自动化系统中使用Python脚本实现,并在最终精炼过程动态执行。
参考文献
1. J.L. Xia and T. Ahokainen, “Transient Flow and Heat Transfer in a Steelmaking Ladle During the Holding Period,” Metallurgical and Materials Transactions B, Vol. 32, 2001, pp. 733–741.2. N.F. Ferreira, B.R. Henriques and D.S. Severo, “The Mathematical Model of CST Pans,” (in Portuguese) ABM Anais do 33rd Seminário de Fuso, Refino e Solidificao dos Metais, 2002, Santos.3. N. Gupta and S. Chandra, “Temperature Prediction Model for Controlling Casting Superheat Temperature,” ISIJ International, Vol. 44, 2004, pp. 1517–1526.4. P.F. Wu, A.J. Xu, N.Y. Tian and D.F. He, “Steel Temperature Compensating Model With Multi-Factor Coupling Based on Ladle Thermal State,” Journal of Iron and Steel Research International, Vol. 19, No. 5, 2012, pp. 9–16.5. P. Samuelsson and B. Sohlberg, “ODE-Based Modelling and Calibration of Temperatures in Steelmaking Ladles,” IEEE Transactions on Control Systems Technology, Vol. 18, No. 2, 2009, pp. 474–479.6. J.R.S. Zabadal, M.T.M.B. Vilhena and S.Q.B. Leit, “Heat Transfer Process Simulation by Finite Differences for Online Control of Ladle Furnaces,” Ironmaking and Steelmaking, Vol. 31, 2004, pp. 227–232.7. A. Gastón, G. Sanchez Sarmiento and J. Sylvestre, “Thermal Analysis of a Continuous Casting Tundish by an Integrated FEM Code,” Latin American Applied Research, Vol. 38, 2008, pp. 259–266.
作者
Franz Ramstorfer(top row, left) Process Senior Manager, Ternium Brasil, Santa Cruz, RJ, Brazil franz. ramstorfer @ternium.com.brBruno Suveges Cerchiari (top row, right) Operations Specialist, Ternium Brasil, Santa Cruz, RJ, BrazilLeonardo Martins Demuner (bottom) Steel Plant General Manager, Ternium Brasil, Santa Cruz, RJ, Brazil唐杰民2023年6月底在安徽黄山屯溪翻译自某国《钢铁技术》今年7月期刊,水平有限,翻译不够准确之处请各位看官给与指正。文中提及到冷钢包和冷中间包受钢问题,不可理解。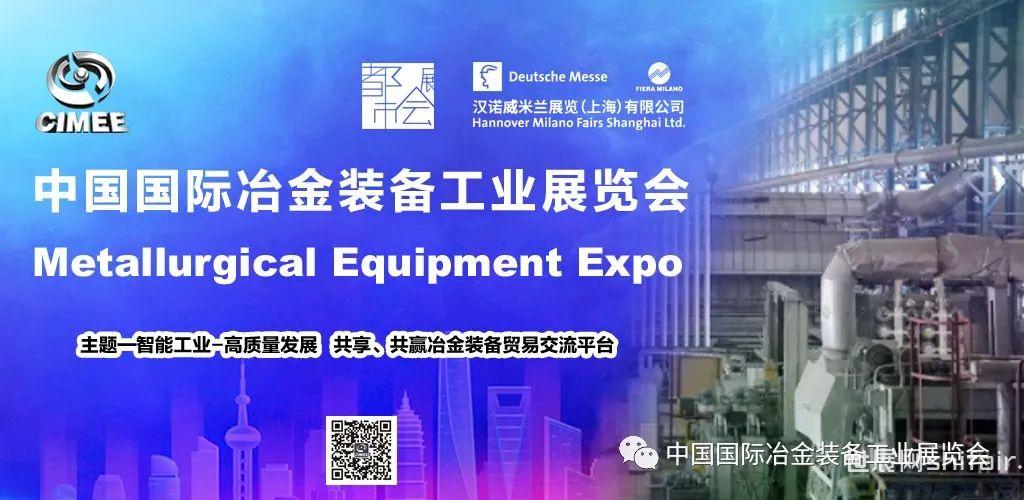