常规低碳钢板坯的高速连铸工艺技术
邓小旋1,2,潘宏伟1,2,季晨曦1,2,初仁生1,2,刘清梅1,2,朱国森1,2
(1. 首钢集团有限公司技术研究院, 北京 100043;2. 绿色可循环钢铁流程北京市重点实验室, 北京 100043)
摘要: 高速连铸具有显著减少建设投资、大幅提高产量和降低物料消耗等优势。但欧、美及国内多数钢厂均使用中低拉速连铸常规厚度板坯,主要原因是高速连铸拉漏风险增加与卷渣导致的表面质量恶化。为解决上述问题,以日本JFE为代表的钢企开发了一系列关键技术,JFE福山No.5 铸机连铸厚度220 mm低碳钢板坯最大拉速达到3.0 m/min。阐述了国内外常规板坯铸机的高速连铸发展历程。基于JFE福山No.5 CCM和首钢京唐No.3 CCM低碳钢高速连铸实践,综述了高速连铸的3项关键技术,分别是强冷却能力结晶器技术、高速连铸结晶器卷渣控制技术和电磁冶金技术,为生产冷轧薄板钢种为主的钢厂提高铸机拉速提供参考。
关键词: 高速连铸;常规板坯;低碳钢;结晶器;卷渣
文献标志码: A 文章编号: 0449-749X(2019)08-0070-12
Review on high speed conventional slab continuous casting of low carbon steels
DENG Xiao-xuan1,2,PAN Hong-wei1,2,JI Chen-xi1,2,CHU Ren-sheng1,2,
LIU Qing-mei1,2,ZHU Guo-sen1,2
(1. Research Institute of Technology, Shougang Group Co., Ltd., Beijing 100043, China;2. Beijing Key Laboratory of Green Recyclable Process for Iron and Steel Production Technology, Beijing 100043, China)
Abstract:Many conventional slab casters in Europe, America and domestic steel companies do not use the high-speed casting although it can significantly reduce the equipment investment, improve the productivity and lower the refractory consumption. The main reasons are the increasing risk of the sticking breakout and the deterioration of surface quality due to the mold powder entrapments at high-speed casting. To solve these problems, Japanese steel companies (eg. JFE) developed a series of key technologies for high-speed casting and the maximum speed of 220 mm-thickness low carbon steel slabs for No.5 CCM at JFE Fukuyama works reached 3.0 m/min. The transitions of casting speeds for overseas and domestic slab casters were presented. In addition, three key technologies (strong primary cooling technology, control of mold powder entrapments and application of electromagnetic equipment at high-speed casting) were reviewed based on the high-speed casting practices for No.5 CCM at JFE Fukuyama Works and No.3 CCM at Shougang Jingtang Works. This review can guide the steel plants to improve their casting speeds whose products are mainly composed of cold-rolled sheets.
Key words:high speed casting; conventional slab; low carbon steel; mold; mold powder entrapment
连铸技术的提出、开发与应用是继转炉炼钢之后的又一革命性炼钢技术,它极大地提高了金属产量,减少了能源消耗。尽管受到薄板坯连铸(CSP、FTSC)和薄带连铸的挑战,常规厚度板坯连铸(220~250 mm)由于压缩比大、生产质量稳定,依然是生产优质板材尤其是高品质冷轧钢板的重要手段。由于拉速是板坯厚度的函数,本文将厚度不低于220 mm、拉速不低于2.0 m/min定义为常规厚度板坯的高速连铸。在满足产品质量的条件下,提高铸机拉速意味着提产增效。高速连铸是一项综合系统性技术,它需要炼钢、精炼、连铸与轧制等各道工序密切配合,互相协作。其优势主要表现在:减少建设投资、设备损耗与人力成本;提高产量,降低成本;减少转炉、钢包与中间包耐火材料消耗,降低转炉出钢温度;减少钢/渣/耐火材料反应时间,提高钢水洁净度。由于碳含量对钢凝固特性影响很大,高速连铸技术集中应用在低碳钢与中碳亚包晶钢,本文仅讨论低碳钢(主要用于冷轧薄板)的高速连铸技术。从世界范围来看,采用2.0 m/min及以上拉速稳定连铸厚度不低于220 mm板坯的铸机主要在日本,包括JFE福山No.5、No.7铸机,JFE仓敷No.4铸机,JFE千叶No.3 铸机,新日铁住金名古屋No.2、鹿岛No.3 铸机和神户加古川No.4铸机。
1、低碳钢板坯高速连铸的难点及相关控制技术分析
尽管高速连铸技术具有前文所述的显著优点和效益,但日本新日铁多数钢厂、美、欧及中国多数钢厂均使用中低拉速连铸常规低碳钢板坯,主要原因在于:(1)铸机冶金长度小、前道工序钢水处理时间长,节奏等因素制约;(2)拉速提高,保护渣消耗量减少,坯壳与铜板之间润滑变差,黏结漏钢风险加大;(3)高速连铸结晶器凝固坯壳变薄,坯壳强度下降,增大漏钢风险;(4)高速连铸结晶器液面波动与表面流速更剧烈,更易卷渣引起轧板线状缺陷;(5)拉速提高,结晶器内夹杂物停留时间缩短,导致其去除率降低,轧板出现缺陷风险增大;(6)在相同条件下,提高拉速延长凝固时间、增大鼓肚量,中心偏析和内部裂纹发生率提高。但需要说明的是,用于冷轧薄板的低碳钢由于压缩比大、钢塑性好,中心偏析等内部质量不是限制拉速提高的主要因素。为解决上述难题,研究人员开发了高速连铸的多项关键技术,包括:(1)强冷却能力结晶器技术;(2)高速连铸漏钢预报技术;(3)高速连铸保护渣技术;(4)高速连铸结晶器流场控制技术(含电磁冶金技术);(5)非正弦振动技术;(6)二冷动态控制技术;(7)低过热度浇铸技术等。1995年王新华等系统综述了日本高速连铸的5项关键技术(2)~(6)。1996年赵兴武等重点论述了技术(3)~(7)。1997年张洪波等综述了高速连铸的3项关键技术,包括技术(1)、(3)和(5)。2007年宝钢蔡宁综述了高速连铸的技术(1)和(3)~(5)。2003年攀钢从达涅利引入国内第一台板坯高速连铸机,随后梅钢、宝钢、马钢、邯钢、首钢均引入了常规板坯高速铸机,并对高速连铸工艺开展了一系列研发工作。前人详细论述了非正弦振动和高速连铸保护渣技术,本文以JFE福山No.5 CCM和首钢京唐No.3 CCM高速实践为背景,综述了国内外高速连铸技术的发展历程并重点论述了高速连铸的3项关键技术,即强冷却能力结晶器技术、高速连铸卷渣控制技术与电磁冶金技术。为生产冷轧薄板钢种为主的钢厂提高铸机拉速提供参考。2、常规厚度板坯高速连铸发展历程2.1国外高速连铸发展历程常规板坯的高速连铸发源于日本。为推行热装轧制和直接轧制,保证连铸与热轧匹配,日本钢企板坯铸机在20世纪80年代中期大幅度提高拉速(图1)。如JFE福山No.5 CCM连铸厚度220 mm板坯拉速从1.6提高至2.8 m/min,最高达3.0 m/min,号称“冠军铸机”。JFE千叶No.3 CCM、新日铁住金鹿岛No.3 CCM、神户加古川No.4 CCM的拉速从常规提高至2.0 m/min以上。部分高速板坯铸机的主要参数见表1,它们具有以下特点:(1)为保证出扇形段铸坯完全凝固,铸机长度均大于40 m;(2)为保证高速连浇过程缓冲和夹杂物充分上浮,配备大容量中间包(60~90 t);(3)为保证结晶器的强冷却能力,结晶器长度范围为900~950 mm。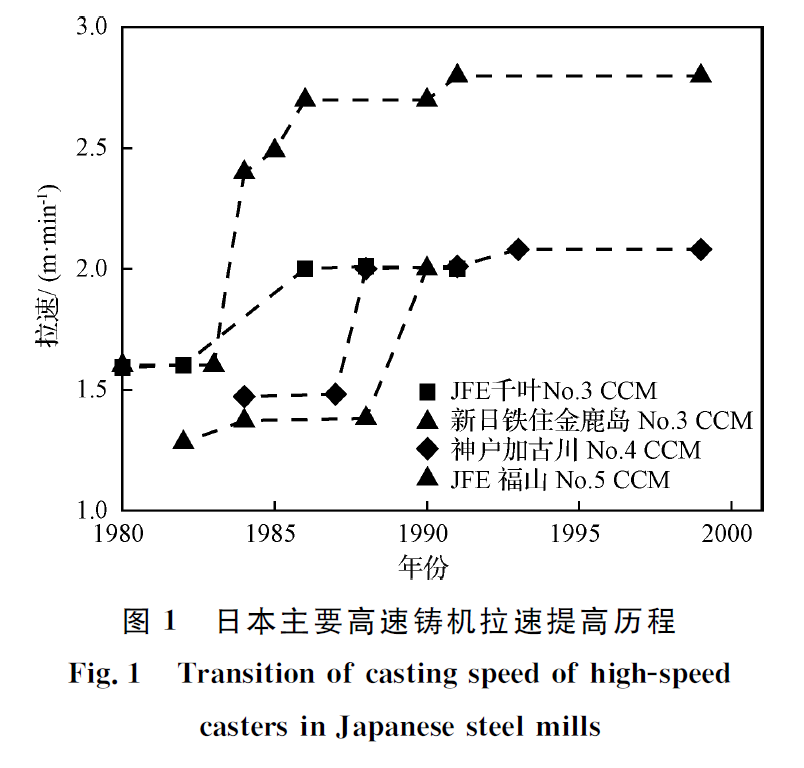
除日本外,韩国、加拿大等地的板坯铸机也开展了提速试验。2007年,浦项光阳No.2-3 CCM由弧形改造成直弧形,改造后铸坯厚度从230增至250 mm,结晶器长度由900延长至950 mm,弧半径由12降至9 m,冶金长度由41延长至47 m;改造后为达到每年350万t汽车外板的目标,拉速从2.3提升至2.5 m/min。加拿大Dofasco报道,为把年产量从140 万t增至170万t,其No.2铸机试验拉速从1.7提高至2.0 m/min。2.2国内高速连铸发展历程国内在2003年前建成的常规板坯铸机拉速为1.1~1.8 m/min,2003年之后新建的几台常规板坯铸机多采用高拉速设计。2003年,攀钢在No.1双流板坯铸机基础上引进了达涅利的No.2单流板坯铸机,并对高速连铸技术开展了较多研究。通过工艺改进,连铸厚度200 mm板坯拉速提高至1.8 m/min,最高达2.0 m/min。据报道,攀钢高速连铸LCAK钢铸坯表面无清理率达90%以上,铸坯w(T[O])控制在0.002 0%以下。攀钢应用高速连铸技术后提高了生产能力,相当于新建1台铸机,减少建设投资3亿~4亿元。同年,梅钢No.2单流铸机投产,该铸机配备FC-mold, 设计最大拉速为2.4 m/min,但2008年增流改造后逐渐降为常规拉速。2006年宝钢No.4铸机投产,主要为1 880 mm轧机供应铸坯。产品覆盖超低碳钢、低合金结构钢等5大品种,最高设计拉速为2.2 m/min。设备采用小辊密排、分节辊布置等先进技术减少鼓肚,但其实际报道拉速低于2.2 m/min。2007年,马钢新区四钢轧总厂投产,其设计产能为150万t冷轧基料。四钢轧No.1铸机配备钢包下渣检测装备、漏钢检测系统、铸坯洁净度判定系统与FC-mold,但其实际仍采用常规拉速,2018年马钢报道其优化了高速连铸浸入式水口结构、FC-mold上下线圈电流等工艺参数,断面不超过1 200 mm拉速提高至1.7 m/min以上。2008年10月,邯宝炼钢厂2台板坯连铸机投产,其No.1铸机设计拉速为2.03 m/min,配备在线调宽、动态轻压下与FC-mold。2010年以前由于受生产节奏影响,拉速低于1.2 m/min,2010年11月,拉速提高至1.5 m/min,但仍低于设计拉速。2009年,首钢京唐钢铁联合有限责任公司(以下简称首钢京唐)投产。立足建立新一代高效、低成本洁净钢平台,首钢京唐采用了一系列新技术。如炼钢采用“全三脱”工艺,RH设计为5级蒸汽泵,67 Pa抽气能力达1 250 kg/h;板坯设计成高速连铸,No.3铸机设计最大拉速为2.3 m/min;配备了多项板坯铸机的先进技术,如液位自动控制、结晶器在线调宽、漏钢检测与预报、动态轻压下与铸坯跟踪等。2012年,首钢京唐与北京科技大学王新华教授课题组合作,对高速连铸结晶器内钢水流动、铜板传热行为、铸坯润滑行为和铸坯表层大尺寸夹杂物表征与控制开展了系统研究。连铸厚度237 mm低碳钢的拉速从1.6提高至2.5 m/min,突破了设计最大拉速。2018年,首钢京唐详细研究了RH高效精炼工艺技术 (SVDC, Shougang developed Vacuum Decarburization)和高速连铸稳定化技术,目前京唐No.3铸机浇铸断面不超过1 200 mm的LCAK板坯拉速稳定控制在1.8~2.0 m/min。国内板坯高速铸机的主要参数见表2,分析认为,它们具有2个共同特点:(1)铸机长度大,除攀钢、邯宝外均大于40 m,设计拉速均不低于2.0 m/min;(2)为保证液面稳定控制,均配备有电磁制动设备(FC-mold)。尽管设计拉速均大于2.0 m/min,但大规模应用中,除首钢京唐No.3 CCM外,其他铸机拉速均小于2.0 m/min。
3、板坯高速连铸关键技术3.1强冷却能力结晶器技术从水口吐出的钢液在结晶器内凝固,形成具有一定厚度的初生坯壳以抵抗钢水静压力而不发生漏钢。高速连铸条件下凝固坯壳变薄,因此必须采用强冷结晶器技术增加初生坯壳厚度。JFE福山No.5 CCM报道其采用强冷结晶器技术的要点为:(1)控制结晶器铜板厚度;(2)合理调整固定螺栓处冷却;(3)增大冷却水流量和流速。采用强冷结晶器等技术后,以拉速3.0 m/min连铸厚度220 mm铸坯的铜板热面最高温度小于350 ℃,有效防止了坯壳与铜板黏结。此外,拉速为3.0 m/min条件下出结晶器坯壳厚度为9.1 mm,但未发生漏钢事故。首钢京唐No.3 CCM为保证结晶器冷却水流速大于9 m/s,将宽面冷却水量从4 610提高至4 900 L/min, 窄面从490提高至600 L/min。采用二维凝固传热模型计算得到出结晶器的凝固坯壳厚度,结果如图2所示。可以看出,坯壳厚度随拉速增大而减小,拉速2.5 m/min对应的窄面出结晶器坯壳厚度为9.5 mm, 与JFE福山No.5 CCM报道的坯壳厚度相当。京唐2.5 m/min拉速浇铸没有发生漏钢事故。此外,首钢京唐低碳钢高速连铸实践中,拉速提高至1.7 m/min后冷却水温差达12 ℃,造成镀层频繁脱落。将水箱进水孔直径从60扩大至80 mm,水温差从12降至8 ℃,解决了镀层脱落问题。
3.2高速连铸卷渣控制技术3.2.1结晶器卷渣发生机理日本学者采用物理模拟详细研究了结晶器卷渣机理,其中以Yoshida J等与Watanabe J等的研究结果最具代表性。卷渣主要有5种方式:(1)流股撞击窄面沿着窄面往上运行,推动保护渣往水口附近移动,导致剪切卷渣;(2)水口左右两侧非对称流场导致水口附近产生漩涡卷渣;(3)吹入结晶器的氩气泡在钢/渣界面破裂,将保护渣裹挟进钢液;(4)钢液表面非稳态流引起的非稳态卷渣;(5)水口出口高速钢流形成的负压区将液态保护渣沿水口外壁吸入,引起卷渣。日本研究的关于卷渣机理及其结论见表3。国内研究人员利用水模型、数值模拟研究了保护渣卷入位置、卷入方式、卷入深度以及工艺参数对卷渣的影响,其主要结论、试验方法等信息见表4。可以看到,国内研究集中在漩涡与剪切卷渣,较少报道气泡卷渣、非稳态卷渣与水口负压卷渣。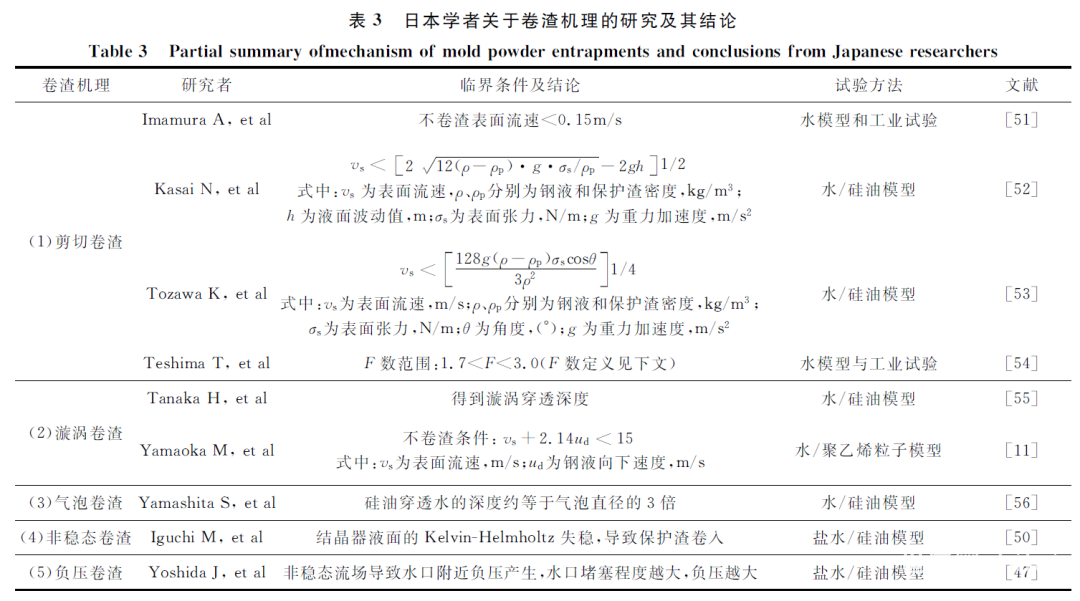
日本学者Teshima T以JFE福山No.5高速铸机为背景,采用1:3的水模型和工业试验研究了板坯高速连铸结晶器内钢水流动行为,提出用液面波动指数“F数”来评价液面波动,作者研究了F数与冷轧卷缺陷发生率的关系,认为F数控制在1.7~3.0时,冷轧卷表面缺陷发生率最低。F数计算公式见式(1)。
式中:ρ为钢液密度,kg/m3;QL为钢液体积流量,m3/s;ve为钢液流股撞击结晶器窄面速度,m/s;α为钢液流股撞击窄边的角度,(゜);D为流股撞击点距弯月面的距离,m。尽管提出了F数,但其仍是一个评价卷渣的间接指标。在高速连铸实践中,主要以液面波动和表面流速来评价。Tsai H T等提出液面波动控制在±3 mm以下时缺陷发生率低,卷渣发生的临界表面流速争议较大,不同学者利用水模型得到的临界表面流速见表3。高速连铸实践中,控制液面波动和表面流速较直接的方法是优化浸入式水口结构和应用电磁冶金技术。3.2.2高速连铸浸入式水口研究浸入式水口结构是连铸过程中为数不多的较易改变且对结晶器流场产生深远影响的参数。浸入式水口结构主要包括水口出口孔数(双孔或多孔)、出口角度、底部形状、出口形状。常规厚度板坯连铸目前主流是采用双孔水口。文献报道常规板坯高速连铸浸入式水口有如下特点:(1)使用大倾角水口有利于降低高速连铸结晶器的液面波动和卷渣风险。曹娜等利用1:0.4水模型研究了梅钢板坯厚度220 mm的高速连铸(最大2.2 m/min)结晶器钢/渣界面行为,认为水口倾角从10°提高至20°,弯月面处液面波动从13.7降至6.2 mm。邓小旋和LI L等利用1:1水模型和数值模拟研究了首钢京唐No.3 CCM高速连铸(最大2.5 m/min)结晶器液面波动和表面流速,认为水口角度从15°提高至20°可有效降低液面波动,并成功应用于高速连铸工业实践。Teshima T等报道JFE福山No.5 CCM在高速连铸(拉速为1.9 m/min,宽度为1 600 mm)使用倾角为45°浸入式水口,认为使用大倾角水口有助于将高速连铸的“F数”控制在合理范围,减少冷轧板缺陷发生率。(2)凹底水口有利于降低液面波动和卷渣概率。文献利用1:1水模型和工业试验研究了首钢京唐No.3 CCM高速连铸下凹底、凸底和平底对液面特征的影响。水模型结果显示,凹底和平底水口的流场对称性优于凸底。水模型和工业试验都表明,凸底水口的液面波动和表面流速均明显大于凹底。因此从减少卷渣角度推荐高速连铸使用凹底水口。文献报道了高速连铸条件下使用5种不同底部形状水口出口流股特征,认为凸底水口出口流股动能大,湍动能小,但凹底水口由于与水口底部作用,动能变弱但湍动能大,有利于消除水口出口的负流区,缓解水口堵塞。(3)水口出口形状没有统一的认识。熊霄等利用1:1水模型对首钢京唐No.3 CCM高速连铸的研究表明,椭圆状水口在高速连铸时流股扩展角和倾角最大,在出口处流速分布均匀,推荐在高速连铸使用。Bai H等认为方形出口流股流速与负流区最大,矩形出口是较优的出口形状。3.3高速连铸结晶器电磁冶金技术应用于常规板坯高速连铸的电磁设备主要包括ABB公司的电磁制动(EMBR,Ruler和FC Mold)和JFE/达涅利Rotelec开发的MM-EMS。高速连铸电磁设备示意图如图3所示。1982年,ASEA(今ABB)和川崎(今JFE)联合开发了第一代局部区域电磁制动技术(Local EMBR),其示意图如图3(a)所示。该设备特点是在2个水口出口区域添加一垂直于流股方向的恒稳磁场,控制从浸入式水口吐出的钢液流股,减轻其对窄边的冲击力度,抑制表面流速和液面波动,降低卷渣概率。川崎水岛厂报道,采用EMBR后,浇铸220 mm铸坯从结晶器SEN侧孔吐出的射流速度降低了50%。1992年,Hoogovens与ABB公司成功开发第二代全幅一段(EMBR-Ruler)技术, 它的特点是安装在靠近弯月面位置,可在全宽度方向上控制结晶器钢水流动(图3(b))。在Hoogovens公司的CC22连铸机上开展试验,结果表明,使用该设备后射流冲击深度从4降至1 m,弯月面温度提高10 ℃,液面波动从5降至3 mm,表面流速从 0.30降至0.15 m/s以下,凝固坯壳厚度增加3 mm,允许拉速进一步提高0.2 m/min。1992年,新日铁开发了LMF(Level Magnetic Field, 图3(c)),该装备与Ruler不同之处在于其安装在水口出口下部,抑制钢液流股对坯壳的冲击,减小下回流冲击深度,在下部形成所谓的“活塞流”。该活塞流动有利于非金属夹杂物和气泡上浮,可有效改善板坯表面质量。Ruler和LMF尽管报道取得了较好的效果,但其制动效果受设备安装位置和浇铸参数影响较大,较少应用于常规板坯的高速连铸。1992年,川崎公司开发了全幅二段电磁制动技术(FC Mold)。该设备特点是由2个覆盖整个宽度方向的水平静磁场构成。FC Mold根据其发展历程分为FC Mold Ⅰ和Ⅱ(图3(d))。FC Mold Ⅰ的特点是上下线圈由同一直流电源控制,不能分开调节磁场强度。FC Mold Ⅱ的上下线圈由不同电源控制,可独立调节。JFE千叶No.3 CCM使用FC Mold高速连铸生产超低碳钢。其报道使用FC Mold后结晶器弯月面温度从1 540提高至1 545 ℃,液面波动大幅度降低,表面缺陷指数从4.5%下降至0.3 %。首钢京唐No.3 CCM在高速浇铸(2.5 m/min)时,使用FC Mold Ⅱ能将结晶器液面波动控制在±3 mm,为提高拉速、保证轧板表面质量奠定了基础。此外,首钢京唐No.3 CCM报道,FC Mold Ⅱ不仅用在高速连铸(≥1.8 m/min),在常规拉速范围(1.5~1.7 m/min)仍可使用。在拉速1.7 m/min条件下,使用FC Mold Ⅱ可将弯月面铜板温度从144提高至175 ℃,钩状坯壳平均深度从2.3降至1.7 mm。焦兴利等研究了马钢四钢轧No.1 CCM浇铸IF钢使用FC Mold Ⅱ的最佳参数,认为该装备上下线圈电流分别为+240 A和-274 A时,IF钢板夹杂物发生率从初期的1.1%下降至0.35%。2013年,ABB公布了其新一代电磁制动设备FC Mold G3,它在第二代(FC Mold Ⅱ)基础上在上磁场附加了交流磁场(图3(e)),可提供3种模式,即直流、交流和组合模式。直流模式:上下线圈都通入直流电源,与FC Mold类似;交流模式:仅上线圈通交流电源,在低拉速使用,在弯月面形成旋转流场冲刷凝固前沿夹杂物,改善表面质量;组合模式:上部线圈通入交流电,下部线圈使用直流电,可降低流股冲击深度,提高弯月面温度等。
MM-EMS的前身为NKK(今JFE)开发的EMLA-EMLS(Electro Magnetic Level Accelerator+ Electro-Magnetic Level Stabilizer)技术。该装置在结晶器高度中部设置了4个电磁发生器,采用交流电源生成4个变化的电磁场(图3(f))。当浇铸速率较低时(较低拉速或窄断面连铸),钢水上回流弱,向弯月面供热不足,容易造成“钩状”坯壳发达,保护渣卷入或气孔等缺陷增多,采用EMLA加速钢水流。反之,在浇铸速率高时(高速或宽断面连铸),钢水流到达窄边附近后形成的上回流过强,容易引起保护渣卷入等问题,此时可采用EMLS对钢水流制动减速。JFE福山No.5 CCM高速连铸采用EMLA-EMLS在拉速和断面变化时的操作情况如图4所示。该厂根据“F数”大小来确定采用EMLA或EMLS。
基于EMLA-EMLS技术,JFE联合Rotelec公司在2003年法国里昂召开的电磁会议上提出了一种自动在线控制系统,称为多模式电磁搅拌器(MM-EMS,即Multi-Mode EMS)。它的开发基于对钢液流场形态控制理念的发展。结晶器内流场形态主要分单股流、双股流和不稳定瞬态流。研究表明,结晶器内强度适中的双股流为最优流态。该设备具备3种电磁冶金功能:(1)EMLA;(2)EMLS;(3)EMRS。前2种功能与EMLA+EMLS相同:当结晶器流场为单股流或较弱双股流时使用EMLA将流场加速成强度适中的双股流;当流场为强度较高双股流时使用EMLS将流股减速成合理强度的流场。第3种功能搅拌结晶器上部的钢液,使其旋转并冲刷凝固前沿的夹杂物/气泡。韩国浦项公司从2001年起对板坯铸机进行改造,在其4台板坯铸机上均配备了MM-EMS。此外,据浦项报道,安装在结晶器中部的MM-EMS在使用其搅拌功能时会与主流股产生干扰。因此,浦项创新开发了可移动的MM-EMS:在使用搅拌功能时将电磁设备移动至弯月面,在使用加速或减速功能时恢复至结晶器中部位置。由于采用了MM-EMS装备等关键技术,浦项光阳No.2-3铸机浇铸250 mm厚度LCAK钢拉速提高至2.7 m/min。从前文论述可知,高速连铸电磁制动设备均朝着“多模式”、“多功能”发展。电流从单纯的“直流、交流”发展成“直流+交流”模式,冶金功能也由传统的“制动”发展成“加速+制动+搅拌”。ABB公司的FC Mold G3和Rotelec公司的MM-EMS是常规板坯结晶器电磁制动设备的典型代表。高速铸机配备的电磁设备见表5。
4板坯高拉速连铸发展展望随着中国经济进入发展转型期,钢铁工业将会面临巨大挑战,主要体现在:企业竞争日趋激烈、降低生产成本压力日益增加、环保限产日益严格。随着高速连铸漏钢预报系统和保护渣技术的进一步发展,高速连铸技术应会成为高品质冷轧薄板生产企业降本增效的有效手段。(1)高速连铸卷渣最直接控制参数是液面波动和表面速度,大倾角和凹底浸入式水口是高速连铸降低液面波动和卷渣的有效手段。(2)高速连铸电磁制动设备均朝着“多模式”、“多功能”发展。电流从单纯的“直流、交流”发展成“直流+交流”模式,冶金功能也由传统的“制动”发展成“加速+制动+搅拌”。ABB公司的FC Mold G3和Rotelec公司的MM-EMS是常规板坯结晶器电磁制动设备的典型代表。(3)尽管以首钢京唐No.3 CCM为代表的常规板坯铸机的拉速取得突破,但高速连铸稳定化技术依然是今后的研发重点。(4)国内常规板坯高速连铸技术的研究主要集中在低碳、超低碳钢等冷轧钢种。亚包晶钢的拉速与日本依然差距较大。亚包晶钢的高速连铸工艺技术将是今后的研发方向。5参考文献略6引用本文邓小旋,潘宏伟,季晨曦,初仁生,刘清梅,朱国森.常规低碳钢板坯的高速连铸工艺技术[J].钢铁,2019,54(8): Xiao-xuan,PAN Hong-wei,JI Chen-xi,CHU Ren-sheng,LIU Qing-mei,ZHU on high speed conventional slab continuous casting of low carbon steels[J].Iron and Steel,2019,54(8):71-80.