New Field Results on Ultrasonic Mold Thermal Mapping for Quality Improvement and Initial Solidification Diagnostics
超声波结晶器热成像技术在结晶器内的应用
Ergolines开发了一种超声波热成像(UT-MAP)系统,可提供结晶器铜管的实时温度图。超声波传感器安装在水套上,仅仅需要最少的加工处理,并且测量是非接触式的。一个专用的UT-MAP软件显示实时温度趋势和弯月面热分布与专用的过程控制工具。从现场数据安装来看,UT-MAP能够检测到铜管热曲线中的异常现象,如粘结粘钢事件和传热变化。通过分析历史温度数据,冶金学家可以优化连铸实践和工艺变量,从而实现可再现的连铸条件,提高铸坯质量。钢液在结晶器内的初始凝固一直是钢铁设备制造商、工程师和学者关注的主要问题,因为这一凝固过程的关键环节对连铸机的性能和铸坯的质量有很大的影响。[1-4]事实上,在结晶器中的第一次凝固初生坯壳对连铸过程的几个关键领域有很大的影响,包括钢厂生产率和钢材质量。生产率在很大程度上取决于结晶器出口的凝固坯壳厚度。当离开结晶器的铸坯固态坯壳能够承受钢水静压时,可以将拉速提高到极限。如果发送漏钢事故,势必损害连铸设备和造成机器停产,从而导致生产的中断。初生凝固对钢坯质量也有很大的影响,铸坯表面和亚表面的完好程度主要取决于在结晶器中发生了什么。同样,许多几何/形状问题,如菱变脱方,可能与结晶器出口初生坯壳厚度不均匀或温度梯度不均匀有关。因此,结晶器铜管的实时热监测是确保工艺均匀性、稳定性和可重复性的有力工具,使用它可以提高铸坯的质量。[7,8]为此,Ergolines开发了一种实时超声波传感器ULD,用于通过超声波非接触式测量铜管的温度。ULD是三种不同结晶器工艺控制工具的基础。结晶器诊断
在竞争日益激烈的市场中,由于工艺问题(偶尔出现漏钢事故、差的产品质量)或机器故障(结晶器变形、保护渣分布不均匀、结晶器振动装置问题)而导致的意外机器停机与生产率降低是随之而来的经济损失的同义词。因此,能够为机器配备旨在预测和规划工艺管理和停机时间的系统变得至关重要。为结晶器配备可靠的传感器和软件工具进行实时系统诊断和在线过程监控的可能性是一个至关重要的竞争因素。因此,钢铁制造商正在寻找能够提供初始凝固过程离线和在线分析的专用工具。离线分析工具主要检测数据相关性,以优化工艺并了解生产损失的原因,包括偶尔的机器停机和相关的经济损失。另一方面,实时分析工具对于有效的结晶器诊断至关重要,可以防止可能出现的问题,如结晶器铜管粘钢和漏钢。因此,通过专门的技术和诊断来解决结晶器中有效的凝固是至关重要的,这也是近几十年来不断增加研发投资的驱动原因之一。结晶器铜管的局部温度与几个关键变量直接相关,包括热流密度、弯月面位置、粘接事件、结晶器润滑、初生坯壳生长、保护渣厚度和保护渣形成夹带物现象(在浸入式水口保护浇铸中)。在弯月面处测得的温度分布实际上与钢液流经结晶器铜管壁的热流有关。结晶器内的热流密度在弯月面区有一个峰值,当凝固条件处于稳态时,热流密度以双曲曲线规律逐渐减小。该热通量峰值通常在4-6 MW/m2左右,在结晶器出口初逐渐降低到小于1 MW/m2。结晶器铜管的温度依次有一个峰值,它位于结晶器弯月面下面。除了许多其他变量外,热流密度与凝固坯壳的厚度和润滑效果直接相关。因此,实时检测相关部位铜管温度的能力为冶金学家提供了关键信息。非接触式结晶器热图
当在结晶器上的多个位置测量铜管温度时,在感兴趣的区域获得“结晶器热图”,这些区域通常是弯月面区域及其下方的区域。结晶器热图提供了关于初次凝固过程和结晶器热状态的关键信息(弯月面位置、凝固坯壳厚度、热流密度、保护渣厚度等)。热量流经由固态坯壳、润滑介质、气隙、固态保护渣、铜管和石灰沉积物组成的一层,直到到达冷却水。热流通常不是恒定的,因为它受到几个因素的影响,例如铸坯坯壳和铜管之间的润滑膜厚度的变化和不均匀性,由于坯壳与结晶器铜管之间的分离导致的气隙,以及结晶器-铸坯界面的物理条件。结晶器热图通常需要侵入式探头,这些探头必须进入到铜管中,例如热电偶(TCs)或光纤(OFs)。TCs和OFs都是“接触式”探头,它们需要与铜管直接接触以测量其温度,因此,TCs和OFs的响应不能是瞬间的,因为它要求探针与铜管达到热平衡,而这个过程需要时间。此外,TC和OF的安装都需要对结晶器铜管进行侵入和昂贵的加工处理,探头必须粘合到铜管上加工的凹槽中,而它们的胶合会引入额外的气隙,从而进一步减慢探头对任何温度变化的响应时间。这种安装的一些缺点影响了备件的成本,因为每个铜管都必须加工。此外,由于存在多个电缆出口,安装很复杂,因为每个TC/ OF探头都有自己的电缆连接到铜管中,每次更换结晶器时必须断开电缆。Ergolines开发了一种基于超声波技术的结晶器热测绘创新系统,该系统以完全“非接触”的方式测量铜管的温度,探头与铜管之间没有任何接触。这是可能的,因为超声波速度取决于温度,因此超声波穿过区域的局部铜管温度可以通过超声波信号的转化来确定。[6,8,9~12,20]由于超声波测量是非接触式的,传感器响应不受达到探头和铜管之间热平衡所需的时间延迟的影响(与TCs和OFs一样),因为“实际”探头是超声波速度本身。因此,与其他现有解决方案相比,应用于结晶器热测绘的Ergolines超声波技术是一项重大改进。非接触式超声波液位检测系统安装
Ergolines的超声波热成像(UT-MAP)系统基于Ergolines ULD传感器,这是一种通过超声波非接触式测量铜管温度的超声波传感器。[20]传感器的尺寸非常紧凑。作为一个关键点,由于传感器安装在水套上,因此安装是非侵入性的(图2)。因此,只需要对水套进行很小的加工处理,铜管保持不变,可以很容易地用标准备用铜管进行更换。
图1 使用ULD传感器的系统(UT LEVEL:结晶器钢水液面控制;UT-MAP:结晶器铜管温度热图;UT-POWDER:保护渣厚度控制和自动添加)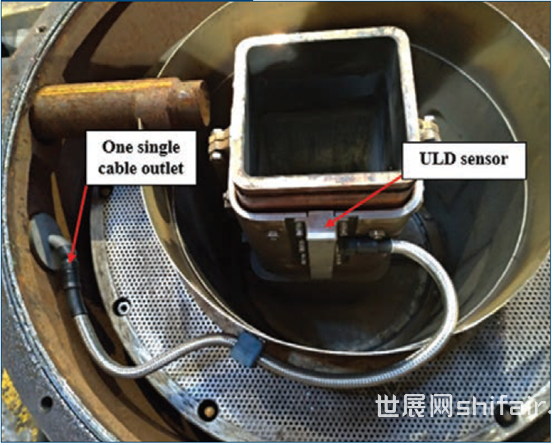
图2 在水套内无妨碍安装Ergolines ULD超声波传感器ULD传感器可以安装在弧形连铸机弯曲的水套上(小方坯结晶器水套,大断面矩形坯或圆坯水套)和板坯结晶器背板上。传感器的机械工程设计上被认为是模块化的。目前有不同的配置,基于1、8、12或16个检测点。16点的ULD模块是一个长度约为40 x 50 x 260mm的小单元。由于传感器的模块化,可以在结晶器上安装多个模块,在一个或多个面,这取决于结晶器要求的面积扩展热图。UT-MAP原则
超声波传感器的工作原理依赖于超声波速度对铜管温度的依赖性。由Ergolines开发的一种基于数学转换和有限元法(FEM)建模的专用算法,可以通过转换超声波信号来确定铜管的温度。在图3的示例中,数据表示弯月面区域几个垂直位置的平均铜管温度。在铜管的冷热面之间的大约2 cm3的铜管体积上取平均值。
图3 超声波测温概念,从左至右为:(1)超声波通过水缝传播;(2)信号处理将超声波信号转换成铜管温度(彩色光束);(3)重建弯月面热曲线(红线)。右图:典型UT-MAP测量区域示意图:铜管温度在弯月面区域垂直绘制通过绘制传感器前每个铜管体积的温度值与沿铜管侧面各自垂直位置的温度值,获得弯月面热图。温度标记为T1, T2,等等,从底部开始,T1在铜管中处于最低位置。Ergolines的UT-MAP系统实时测量铜管的温度趋势和弯月面热图(图4)。
图4 超声波传感器测量铜管温度数据的示例:每个温度测量的位置在图表上方的图表中表示该系统能够检测到被测体积的微小温度变化,因为超声波以高频和超声波速度从内到外管壁穿过整个铜管的体积。传感器每秒测量几次温度值,提供有关热面上发生的情况的实时信息(例如,与瞬时温度变化相对应的钢水液位波动)。ULD过程控制工具和诊断应用
ULD传感器作为基本技术组件集成到三种不同的工艺工具中:UT-POWDER(保护渣厚度控制和自动添加),UT-LEVEL(结晶器钢水液面控制)和UT-MAP(结晶器铜管温度映射图)。UT-POWDER是用来自动控制保护浇铸中的结晶器保护渣厚度,如前所述的论文。[6-21]当结晶器钢水液面由辐射传感器控制时,来自ULD的信号可以作为反馈来控制Ergolines的自动保护渣给料器(MPF),保持结晶器内保护渣厚度恒定。在结晶器中保持恒定润滑的好处已经在几家工厂得到了证明,提高了工艺的可靠性、可重复性和铸坯的表面质量。UT-LEVEL是替代辐射式钢水液面控制,而且领先一步,它带来了非辐射式组件的所有安装优点。该系统实时提供钢水弯月面的位置,并与塞棒或拉矫机控制连铸拉速。目前,该系统安装在CCM中,采用的是敞开浇铸方法,该系统已被证明是可靠的和一致的。UT-MAP是第三种工具,可以提供结晶器热剖面和铜管温度趋势的实时信息。这一关键信息可以作为正确凝固、稳定工艺和优化连铸参数设置的指标。诊断工具UT-QUALITY TRACKING使用的标准偏差,提供钢坯的质量跟踪和基准,指示产品的温度偏差或突然温度峰值发生的部分,可能是由于粘结粘钢或漏钢,异常液位波动,不正确的浸入式喷嘴(SEN)位置,不正确的润滑等造成的。UT-MAP有很大的潜力成为结晶器初生坯壳凝固问题的重要预测诊断工具。该工具可以在线用于实时过程控制和诊断,也可以离线用于过程设置的优化。超声波热成像系统作为实时过程控制,利用结晶器热成像信息来识别与初始凝固有关的可能问题,并提出防止漏钢和粘接事故的措施。如果ULD安装在多个结晶器面上(即所有矩形坯的四个面),则应用程序变得非常强大和高效。UT-MAP可用于在线生成凝固参数偏离标准或快速变化的警告,以增加过程的可靠性和均匀性,对产品质量都有有益的影响。如果将超声波热成像系统用作简单的数据记录仪,则可以使用离线分析方法进行工艺优化和问题分析,并通过分析来找到排除故障的方法,例如,了解漏钢或质量问题的成因。UT-MAP数据的离线分析提供的进一步好处包括设备的预测诊断,例如,铜管状态(厚度、变形情况、锥度磨损)、保护渣给料系统(一致性和可重复性)、结晶器对中、铜管内腔弯月面附近的石灰垢层、结晶器铜管外弧与空间弧对中和中间包过热度效应。现场的结果
众所周知,固态凝固坯壳在铜管壁的粘滞可能导致严重的问题,从铸坯的表面缺陷到漏钢。这种粘连是由固态坯壳断裂造成的,这导致钢液从凝固坯壳中流出,并局部粘附在铜管上。一般来说,固态坯壳表面和铜管内腔表面之间的粘连可能是由大的液面波动、突然的速度变化、过高的连铸拉速或润滑不良引起的。当碳质结块(由未熔化的结晶器保护渣或SEN/中间包耐火材料的侵蚀脱落形成)阻止了液态保护渣流入铸坯与铜管壁之间的间隙时,也可能发生粘连。由于粘接引起通过结晶器铜管壁的热流密度的局部变化,粘接事件可以通过分析弯月面处的热图形状来识别。弯月面处的正常温度曲线显示其下方有一个单一的传热峰值,然后由于初生固态坯壳的形成及其逐渐收缩脱离铜管内腔,其铜管温度平稳下降。相反,粘着事件通常表现为温度峰值以下区域的“热点”,钢液从一个小的坯壳断裂中涌出,并直接与铜管接触,导致铜管局部过热(热点)。当铸坯由拉矫机引导离开结晶器,粘着物随着铸坯向下运行,热点向下移动,其速度就等于连铸拉速。这种机制是典型的粘性机制,可以被认为是铸坯抗议的“签名”。如果不立即采取适当的纠正措施,粘连可能会演变成漏钢。降低漏钢风险的一个可行策略是在发现粘接后立即降低连铸拉速。这种对策为坯壳的生长和坯壳断口重新闭合提供了更多的时间。固态坯壳变得更厚,因此可以承受结晶器出口的钢水静压,从而避免了破裂漏钢事故的发生。现场结果:漏钢分析-例1
现场数据来自一家钢铁厂,在那里用UT-MAP测量了现场的结晶器铜管温度。这个例子显示了在连铸拉速下,发生在结晶器内的粘着是如何被检测到的。图5中的图形显示了在软件中出现的正常连铸浇铸的过程。橙色线是由辐射传感器控制的钢液面,而其他趋势是铜管的实时温度。右边的黄色曲线为UT-MAP测得的弯月面处瞬时温度曲线(x轴为铜管温度,y轴为沿结晶器测温的垂直位置)。曲线对应于光标所在的时间瞬间(趋势图上的垂直黄线)。曲线的形状是典型的正常浇铸的条件:在弯月面略下一点的地方有一个特征温度峰值(低于弯月面约20mm),然后由于凝固固态坯壳形成时的收缩造成逐渐脱离铜管内腔壁,温度下降。温度峰值相当“圆润”(不尖锐),温度趋势显示低噪声且稳定,对应于规则且稳定的弯月面。另一方面,图6显示了漏钢造成的连铸停止过程。将其与图5进行比较,可以立即清楚地看出,温度趋势噪声更大,具有高振幅振荡和频繁出现的峰值,反映了弯月面的显着不稳定性。此外,弯月面曲线有一个异常的形状,具有一个非常尖锐的峰值,相对于图5的位置低得多。峰值位置较低的事实意味着由于过量的结晶器保护渣,钢弯月面实际上在结晶器中较低(众所周知,辐射传感器将保护渣视为钢水液面的虚假增加,因此其反馈降低了实际钢水液面:保护渣厚度越高,钢的弯月面越低)。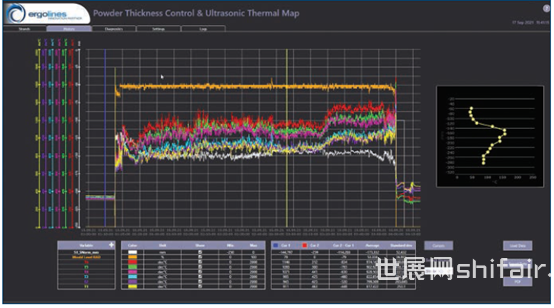
图5 正常的连铸过程和正常的热面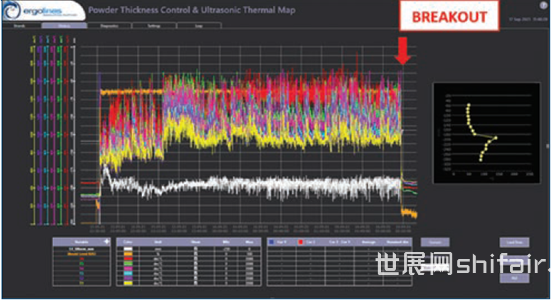
图6 漏钢过程:温度不稳定出现漏钢通过放大漏钢前最后10分钟的趋势(图7),可以观察到弯月面(红色箭头)下温度的几个突然振荡。此外,在漏钢发生前一分钟,可以看到一个明显的温度振荡,在温度趋势上具有典型的交叉模式,这代表了粘着事件的特征。[8]事实上,在正常连铸条件下,温度趋势是相互平行的。另一方面,当粘接发生时,温度趋势相互交叉,因为粘接(热点)以等于连铸拉速逐渐被拖下结晶器。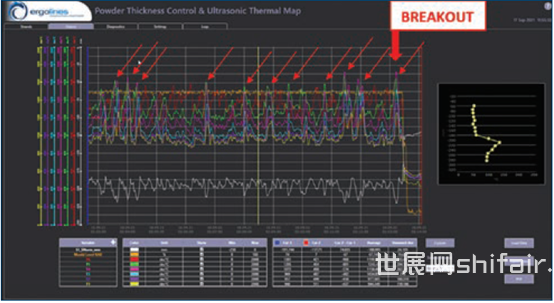
图7 图6放大特写,漏钢前的十分钟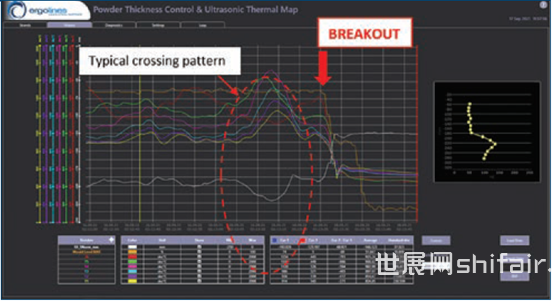
图8 图6放大特写。漏钢前一分钟综上所述,图6-8的UT-MAP数据显示,连铸条件并不理想,弯月面区域明显不够稳定,导致夹杂裹挟或粘接,这可能是由于几个因素造成的,包括使用某种保护渣类型和在某种钢种上,以及非最佳连铸机工艺参数(如水冷却参数)或操作上不够完美。现场结果:漏钢分析-例2
作为基于UT-MAP数据的漏钢分析的第二个例子,图9底部的图表显示了另一个漏钢事件发生前一分钟的温度趋势。通过将趋势与温度曲线(图9顶部)相关联,提出了以下机制来解释结晶器内可能发生导致漏钢的原因:
图9 漏钢前一分钟的UT-MAP数据图中:1连铸开始正常浇铸状态:在弯月面下方典型的高温峰值;2 添加过多的保护渣造成弯月面下降(这是由于辐射检查液面所致);3 当弯月面再次上升,造成块状固态保护渣进入,ULD发现在这个保护渣形成的大型夹带渣前面的铜管壁出现冷区;4 这个保护渣大型夹杂随着拉速下降,辐射液面检测到液态保护渣,ULD能够再次看到弯月面;5 这个大型夹带渣引起了固态坯壳开裂,离开结晶器后发生漏钢。通过分析UT-MAP数据,可以估算出保护渣形成大型夹带物形成的时间。结晶器长度为1000mm,弯月面距距离铜管顶端为150mm。连铸拉速为1.6 m/min或26.7 mm/ s。因此,这个大型夹带物大约需要32秒才能到达结晶器的出口。在图9底部的图形中,每一水平划分为5秒,在离开结晶器前32秒对应ULD传感器前铜“冷”的时间间隔,这与夹带物的形成一致。因此,这一估计与辐射测量的结晶器液面和ULD温度趋势分析是一致的。根据这些结果,检测和防止漏钢的可能解决方案可能是:当辐射计测量到结晶器液面突然增加,同时ULD检测到弯月面位置非常低(意味着保护渣过量),自动化可以向操作员显示警告信号:可能已经形成固态保护渣夹带物,坯壳可能受到损伤。降低浇注速度可避免漏钢。操作员(或直接自动化)可以降低连铸拉速,以便在夹带物到达模具出口之前让损伤开裂的坯壳再次凝固。这样,应该可以防止漏钢。现场结果:漏钢分析-例3
报告了如何使用UT-MAP数据来检测和预防漏钢的另一个例子。图10显示了漏钢前7分钟用UT-MAP系统测量的6个温度分布序列。
图10 第二个峰值(红色箭头)逐渐出现在弯月面峰值(橙色箭头)下方(2)。第二个峰代表粘着热图显示了超声波传感器如何将粘着视为沿结晶器向下移动的“热点”:最初的如图曲线是正常的,由于钢的弯月面(橙色箭头)形成一个单峰,由于固态坯壳收缩逐渐脱离铜管内壁形成气隙,温度逐渐下降。第二个峰(红色箭头)逐渐出现在半月板峰值(橙色箭头)下方。第二个峰值代表了粘滞。当铸坯被拉矫机下行引导时,保护渣夹带物以与相同的连铸拉速沿着结晶器被拖拽带下:温度曲线清楚地显示了第二个峰值沿着结晶器向下移动(红色箭头)。粘着处(红色箭头)进一步沿着结晶器向下移动,而半月板峰值(橙色箭头)保持稳定,因为没有钢水液面的修正。夹带物在传感器下方移动。夹带物完全位于传感器下方,检测不到夹带物,因此只能看到弯月面峰值。此粘接事件发生在漏钢前6分45秒,随后停止浇铸生产。因此,在粘接事件和漏钢之间的时间间隔中,钢坯以3.5米/分钟的拉速移动了23米。必须注意的是,传感器只能检测安装位置上的结晶器表面发生的事件。因此,实际导致漏钢事件可能是与UT-MAP观察到的类似的另一个粘附事件,但发生在稍后的不同结晶器表面。即使检测到的粘接事件不是导致漏钢的原因,数据也表明连铸条件并不理想,可能导致频繁的粘接事件,最终演变为漏钢。现场数据分析清楚地表明,UT-MAP数据可用于检测异常连铸状况,可能导致粘接事件和保护渣夹带物。作为未来的发展,可以通过专门的算法检测粘接“双峰”,并自动向该流铸坯可编程逻辑控制器(PLC)发送“粘接检测警报”,使操作员能够采取适当的纠正措施,如降低连铸拉速,为凝固固态坯壳再次形成提供足够的时间,并闭合断裂处,从而避免漏钢事故的发生。综上所述,利用超声热成像数据可以实现:现状:离线分析过去多次粘接事件与工艺条件的相关性,如结晶器铜管寿命,钢种,保护渣类型和消耗量,连铸拉速的选择,以及跟踪坯的质量控制分析。通过分析历史超声热成像数据,冶金学家可以系统地识别连铸过程中的异常,并优化连铸工艺参数,以提高钢的质量。未来发展方向:在线自动检测粘滞事件,实时报警。粘连事件由专用算法自动识别,并将粘连检测警报发送到链PLC,然后可以自动执行诸如降低连铸拉速之类的纠正措施。结论
Ergolines开发了一种用于结晶器实时超声热成像(UT-MAP)的新系统。该系统基于ULD传感器,采用超声波技术以全非接触方式测量铜管的温度。该系统在水套中安装简单且无破坏性,可提供有关传热和凝固行为的实时关键信息。ULD可以很容易地安装在弧形连铸机结晶器弯曲的铜管(小方坯钢坯和大断面矩形坯)和板坯结晶器的背板上。报告的现场结果表明,UT-MAP数据在粘接检测方面的有效性,以及它作为一种漏钢系统的未来发展潜力。UT-MAP是实现预测模具诊断的关键工具,可以实时控制初始凝固,并可能防止粘连和漏钢等危险事故发生。
参考文献
1. Thomas, B.G., “Modeling of Continuous-Casting Defects Related to Mold Fluid Flow,” 3rd Internat. Congress on Science & Technology of Steelmaking, 2005.2. Thomas, B.G., “On-Line Detection of Quality Problems in Continuous Casting of Steel,” Modelling, Control and Optimization in Ferrous and Nonferrous Industry, 2003.3. Lait, J.E., and Brimacombe, J.K., “Solidification During Continuous Casting of Steel,” Continuous Casting, Vol. 2, 1984.4. Emi, T., Surface Defects on Continuously Cast Strands, The AISE Steel Foundation, Pittsburgh, Pa., USA, Ch. 21, 2003.5. Ecke, W., “Applications of Fibre Bragg Grating Sensors,” IPHT Jena, The 19th International Conference on Optical Fibre Sensors, 2008.6. Schiavon, G.; Spagnul, S.; Mazza, I.; and Miani, S.; “Recent Improvements in Real-Time Thermal Mapping of Copper Mold With Ergolines Ultrasonic Sensor,” Proceedings of 5th ESTAD, 2021.7. Scarabelli, C.; Olivero, D.; Bego, F.; Spagnul, S.; Mazza, I.; and Schiavon, G., “Powder Dosing With Mold Temperature Feedback Control in Continuous Casting of Stainless Steel for High Quality Billet Surfaces,” Proceedings of ECCC, 2020.8. Mazza, I.; Miani, S.; Schiavon, G.; and Spagnul, S., “Fully Contactless Mold Thermal Mapping and Breakout Prevention for Billets and Blooms: An Innovative System to Improve Metallurgy, Quality and Productivity,” AISTech 2019 Conference Proceedings, 2019.9. Spagnul, S.; Mazza, I.; Miani, S.; and Schiavon, G., “Breakout Prevention for Billets and Blooms Through Contactless Mold Thermal Mapping: A New Tool for Metallurgists, Quality Control and Productivity Improvement,” Proceedings of METEC, 2019.10. Mazza, I.; Miani, S.; Schiavon, G.; and Spagnul, S., “Real-Time and Contactless Mold Thermal Monitoring: Improving Metallurgy, Quality and Productivity of Billets and Blooms,” Proceedings of ESSC and Duplex, 2019.11. Mazza, I.; Miani, S.; Schiavon, G.; and Spagnul, S., “Contactless Mold Thermal Mapping at Meniscus Through an Innovative Ultrasonic Sensor,” Proceedings of ICS, 2018.12. Mazza, I.; Miani, S.; Schiavon, G.; and Spagnul, S., “The Mold Temperature Mapping With Ultrasonic Contactless Technology Is the Key for the Real- Time Initial Solidification Process Control Tools,” Proceedings of ECCC, 2020.13. Spagnul, S.; Olivo, L.; Schiavon, G.; and Mazza, I., “A Compact Mold Powder Diffuser With Built-In Optical Powder Thickness Measurement,” Iron & Steel Technology, December 2017, Vol. 14, No. 12, pp. 64–70.14. Mazza, I.; Spagnul, S.; Olivo, L.; and Milani, F., “Review of Technologies and Methods for Mold Powder Thickness Control,” La Metallurgia Italiana, No. 4, pp. 30–37.15. Spagnul, S.; Olivo, L.; Schiavon, G.; and Mazza, I., “A New Instrumented Mold Powder Diffuser With Built-In Optical Sensor for Powder Thickness Control,” Proceedings of ECCC, 2017.16. Olivo, L.; Spagnul, S.; and Mazza, I., 2016, A New Optical System for Mold Powder Thickness Control by Laser Scanning and Multi-Spectral Imaging,” Iron & Steel Technology, December 2016, Vol. 13, No. 12, pp. 62–69.17. Mazza, I.; Spagnul, S.; and Mantovani, F., “Review of the Mold Powder Control Technology,” Proceedings of METEC, 2015.18. Spagnul, S.; Padovan, M.; Bianco, A.; and Mantovani, F., “Latest Enhancements in Mold Powder Thickness Control as a Result of a New Propulsion System Implemented in Flux Feeding,” Proceedings of ECCC, 2014.19. Spagnul, S., and Mantovani, F., “A Reliable Powder Control Based on an Automatic Closed Loop System Including Measurement, Powder Feeding and Powder Thickness Control,” Proceedings of METEC, 2011.20. Mazza, I., and Spagnul, S., A Novel Ultrasonic Sensor for Mold Powder Thickness Control,” Proceedings of METEC, 2015.21. Spagnul, S.; Mazza, I.; Schiavon, G.; and Miani, S., “An Innovative Ultrasonic System for Steel Level Control,” Proceedings of 7EFRS 2019, International Iron and Steel Symposium, 2019.22. Mazza, I; Miani, S.; Schiavon, G.; and Spagnul, S., “The Mold Temperature Mapping With Ultrasonic Contactless Technology Is the Key for the Real Time Initial Solidification Process Control Tools,” Proceedings of ECCC, 2021.
作者
Giovanni Schiavon:Ergolines Lab s.r.l., Padriciano, Trieste, ItalyStefano Spagnul:Ergolines Lab s.r.l., Padriciano, Trieste, ItalyIsabella Mazza:Ergolines Lab s.r.l., Padriciano, Trieste, ItalyStefano Miani:Ergolines Lab s.r.l., Padriciano, Trieste, Italy
唐杰民2023年9月初在安徽黄山屯溪翻译自某国《钢铁技术》本月期刊,水平有限,翻译不够准确之处请各位看官给予谅解和指正。值得一看的文章
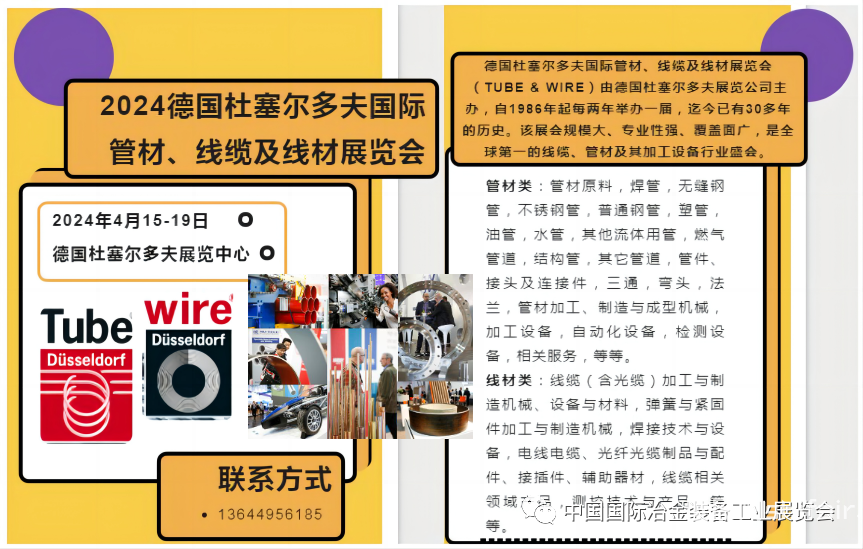
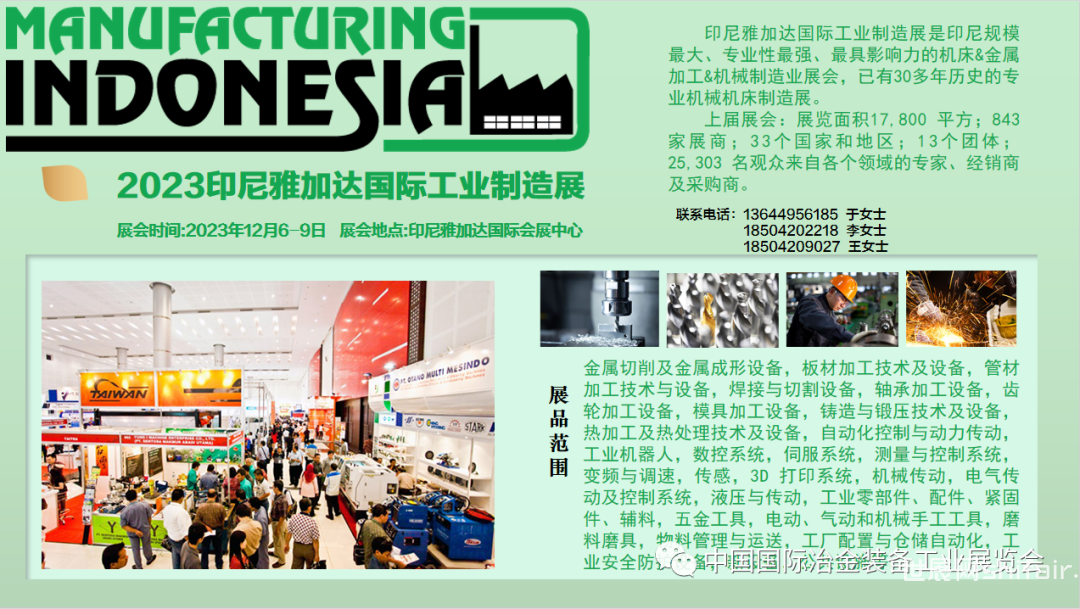
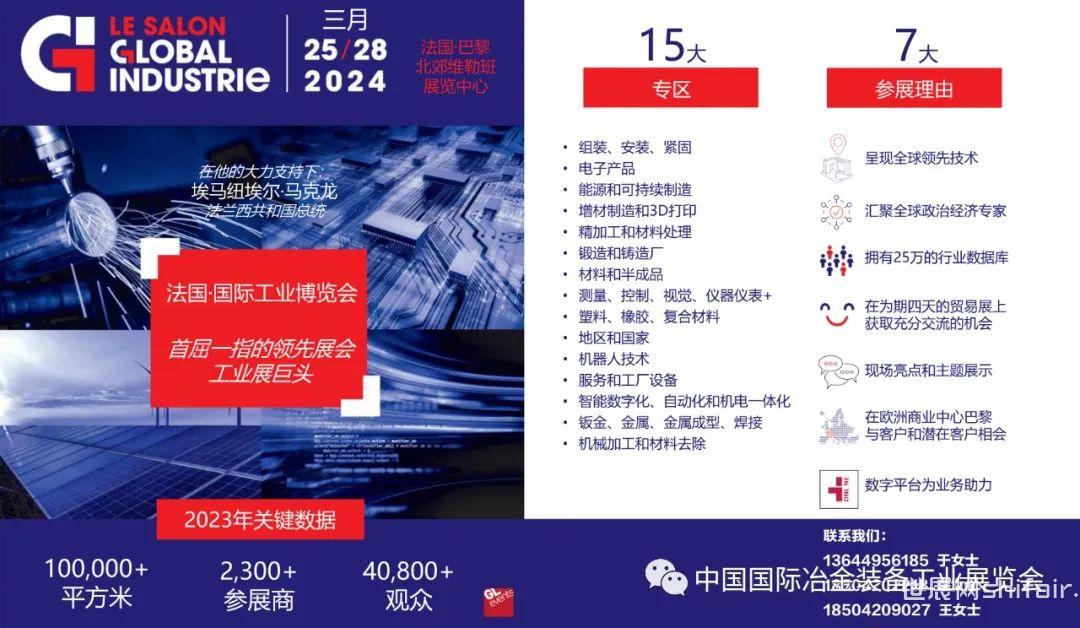
会务组联系方式 电话微信:13248139830(展商名录咨询)