摘要:对DR检测、脉冲涡流检测、阵列涡流检测和超声导波检测在LNG低温管道无损探伤中的适应性进行研究,实验发现,4种检测方法对于不同管径和保温层厚度的低温管道具有不同的缺陷检验效果,结果可为低温环境中特种设备的检测提供指导,及早排除安全隐患,保障其安全运行。关键词:低温管道,无损检测,适应性分析,LNG接收站近年来,LNG接收站建设的速度逐渐加快,导致站内低温压力管道的检验检测工作与日俱增。LNG接收站主工艺系统管道为不锈钢材质,均在深冷工况(工作温度-162℃左右)下工作,主要由5部分组成:卸料系统由气相返回臂、液相卸料臂等组成,负责LNG卸船至接收站;储存系统是LNG低温储罐;BOG处理系统分为将蒸发气直接输送至燃气管网的直接输出法以及通过再冷凝器中低压输送泵后和来自储罐的LNG混合输出的再冷凝法;输送系统是LNG从储罐中泵出,经高压泵加压后输入蒸发系统,经计量后输送至外部管网的过程;汽化系统通常使用海水开架式蒸发器将LNG进行汽化之后再进行输送,其中开架式蒸发器运行成本低、可靠性高。LNG解决了城市能源问题,但在储存和运输过程中存在一定的危险性,一旦发生事故后果将十分严重。2011年江苏徐州LNG加气站储罐底部出现泄漏,遇居民燃放烟花引发大火,火焰高逾20m。2004年阿尔及利亚Skikda液化天然气发生火灾事故,共造成27人死亡,56人受伤,损失高达9亿美元。因此,定期无损检测对保障LNG接收站低温管道安全运行至关重要。按照TSGD7005—2018《压力管道定期检验规则——工业管道》的规定,压力管道均需定期进行检验。由于LNG接收站管道运行条件特殊(工艺温度-162℃左右),材料为奥氏体不锈钢,随着站内低温管线运行时间的延长,不可避免地会产生一定的安全隐患,而主工艺系统均在深冷工况下运行,给检验工作带来较大困难[5]。如何在检验周期内发现低温管道的安全隐患,不仅关系着整个接收站的安全性,更涉及到区域能源供应的稳定性。笔者采用DR检测、脉冲涡流检测、阵列涡流检测和超声导波检测这4种无损检测技术对LNG低温管道进行检测,分析各检测方法的适应性,为LNG接收站内低温管道的无损探伤提供实际工程指导,对保障其长时间安全稳定运行具有重大意义。1 DR检测目前,DR检测技术已成功应用于高、低温工业管道的无损检测,与传统X射线检测相比,DR检测技术更加准确可靠。本实验采用美国GE公司生产的ISOVOLT320M2hp型射线机,采用XRD0822型平板探测器,根据现场不同的实验条件,选用适宜的透照方式和参数,对不同管径的低温管道进行DR检测。通过调整DR检测系统透照等工艺参数,使得检验精度满足相关要求,对所测管线进行编号,标定缺陷位置,采集基础数据。图1为DN50mm的LNG低温管道DR检测照片,可以看出,DR检测可直观检测出管道内腐蚀位置,且管道内部成像质量较高。可能是由于缺陷本身尺寸较小所致,对于裂纹类缺陷的检测结果有效性较低,且裂纹缺陷对于射线检测属于易漏缺陷,但可以通过图像锐化、对比度增强等手段进行处理,以增强可视效果。
为了研究LNG低温管道管径对DR检测精确性的影响,分别对LNG站场内DN80、DN150、DN200mm管道进行DR检测,DR检测照片如图2所示。LNG站场低温管道在线检测时,保温层厚度对DR检测精度的影响不大,在一定条件下,DR检测可以高效地判断和识别出管道内部缺陷。对于DN200mm以下的低温管道,DR检测可以清楚地识别错边缺陷位置,对于未焊透和未融合缺陷也具有较好的检出效果,并且能清晰辨别缺陷区域位置及尺寸;对于DN200mm以上的低温管道成像质量较为清晰,但焊缝缺陷位置不易观察,因此可采用更强大、有足够穿透力的射线源,以获得高质量、可清晰识别的缺陷图像。2 脉冲涡流检测LNG站场低温管道属于非铁磁性材料,满足脉冲涡流检测的要求。基于脉冲涡流的无损检测技术不需要拆除所测管段的保温层,极大地提高了工作效率,实现了管道的在线检测。实验采用OktantaPE4332型脉冲涡流检测仪,对现场带有保温层的低温管道进行管壁测厚和缺陷评估,结果如图3所示。可以看出,当保温层厚度在100mm以下时,检测数据较稳定,可以有效扫查管道壁厚。当保温层厚度在100~150mm时,实验数据不稳定,出现跳跃点,当保温层厚度达到200mm以上时,则无法进行检测。脉冲涡流检测可以有效判定LNG站场低温管道的完整性,实现对低温管道壁厚的测量,进行缺陷尺寸的评估和缺陷类型的识别,并对所检测试件表面下深层裂纹的定量检测具有良好的适应性。在实际工程应用中,脉冲涡流检测可以根据不同缺陷数据进行曲线绘制,测得缺陷最大值后确定对应缺陷深度,因此对于检验条件较苛刻的特种设备,脉冲涡流检测具有较强的适应性。
3 阵列涡流检测管道近表面裂纹可采用ZetecMIZ-21C型阵列涡流检测仪进行检测,现场检测需拆除保温层,用检测探头对管道表面进行环向及轴向扫查。常规涡流检测对于特种设备具有局限性,而阵列涡流检测技术是一种将若干涡流线圈有序排列从而进行大面积扫查和直观显示的新型表面涡流检测技术,因此对于不锈钢材质管道的检测具有良好的适用性,现场检测示意图如图4所示。
采用阵列涡流检测技术对LNG站场内低温管道进行检测,通过调整适宜的检测参数,可以有效实现对低温管道近表面缺陷的无损检测。从图5可以看出,低温管道母材和弯头处阵列涡流检测信号并无异常,信号曲线平整、光滑,信号能量无突变点,扫查图像直观可靠。但阵列涡流检测无法呈现缺陷的形貌特征,这是由阵列涡流线圈特性所决定的,难以表现局部细节,但可以通过增大显示对比度对缺陷进行评价。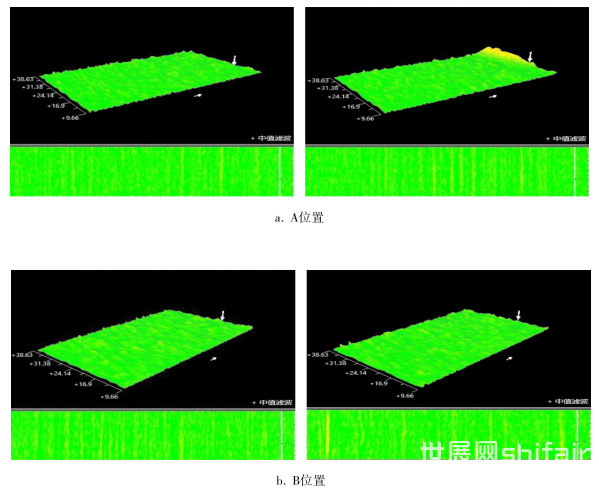
4 超声导波检测对管道本体的缺陷检测采用SRT型超声导波检测仪,在去除保温层的情况下,现场实验根据不同管径的大小,调整导环固定带至适宜长度,使探头与管道表面良好耦合,对低温管道进行超声导波检测。由于超声导波检测技术的局限性,在弯头、法兰和支架处其信号会发生叠加而影响检测结果的准确性,因此现场选用低温管道的直管段进行检测。基于超声导波的无损检测技术可以更高效地对管道本体进行全面扫查,检测管道覆盖面积较大,同时几乎不受管道外径尺寸影响。检测时利用铁钴带将传感器与管道表面紧密贴合,选用扭力波激发模态,以便获得较高的分辨率,所得检测结果如图6所示。
由图6可以看出,总体上波形中所包含的信号特征较少,仅存在管道焊缝、弯头及法兰等相对较明显的信号特征,而其他信号特征在波形图中并无清楚表达,且信号能量值偏小,导致无法准确判断所测管件的相对完整性。这主要是由于接收站内LNG管道表面温度过低而导致传感器性能无法正常发挥或传感器与管道表面无法良好耦合,因此基于现有的技术条件,LNG站场内低温管道的超声导波检测并不具备良好的可行性。5 对比分析以上4种无损探伤检验检测方法的优缺点对比见表1,可以看出,DR检测、脉冲涡流检测和阵列涡流检测均具有良好的检测效果。DR检测可精准标定缺陷位置且管道内部成像质量较高;脉冲涡流检测效率高,可测保温层厚度达200mm;阵列涡流检测可大面积扫查并直观显示。超声导波对于LNG管道检测效果不佳,且弯头、法兰和支架处检验受限,无法满足管道表面缺陷评价的要求。
6 结束语由于LNG接收站内管道的低温特性,检验条件特殊,且国内外在LNG接收站内低温管道的检验检测方面标准规范并不完善,缺少相关经验,应尽快补充,并满足LNG接收站压力管道的相关检测要求,对保障在役LNG接收站低温管道的安全运行具有重要意义。吴斌、张皓、张大伟等发表于《化工机械》第50卷第1期
免责声明:
1、图文素材部分来源于网络,版权归原作者所有,如有侵权,请联系删除。
2、信息内容仅供学习、参考,并不代表赞同其观点。不对信息准确性、可靠性或完整性负责。
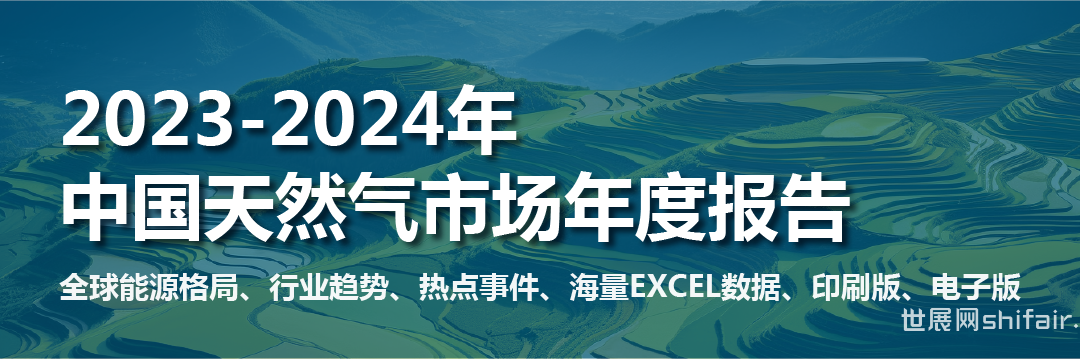


旨在分享,亦尊重版权。LNG行业信息本平台转载上述内容,对文中陈述、观点判断保持中立,不对所包含内容的准确性、可靠性或完整性负责,仅供参考,风险自负,如有侵权请联系删除。如有投稿欢迎联系电话/微信:246刘。
会务组联系方式 电话微信:13248139830(展会咨询)